Why Is Technical Content So Passive?

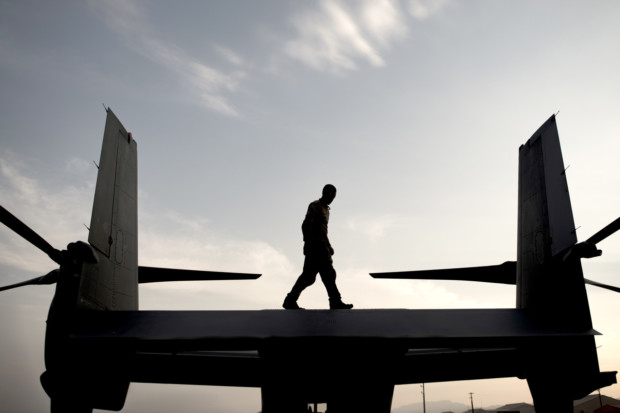
Take the Aerospace and Defense sector as an example. In their ongoing quest to reduce asset maintenance time and increase asset availability, management teams have always focused on optimizing approaches for labor assignment and part allocation. Unfortunately, this focus has ignored another key component to reducing downtime and increasing availability – technical publications.
Technical publications define the proper operations and maintenance for an asset. This collection of documents sits waiting to be used by an operator or technician.
When failures occur, someone needs to:
- Dispatch labor.
- Diagnose the issue.
- Locate the repair procedure.
- Locate the replacement part(s).
- Locate the tools.
And finally, hope the technician dispatched has the right skills to perform the repair.
Harnessing knowledge
Technical publications hold critical information, representing best practices and institutional knowledge for the proper operation and maintenance of the asset. But the operator, maintenance analyst or technician needs to search for and pull in these diagnostics checklists, repair procedures and visually interactive diagrams.
These technical documents contain not only the step by step procedures, but also contain information on the parts, tools and skills required for a given activity. Technical publications content should and can play a much more proactive role in the next generation of advanced maintenance concepts.
How can technical publications play a more proactive role in the maintenance processes?
Today’s modern assets can have embedded systems that monitor asset operations with standard operating parameters and detect emergent issues in real-time when asset behavior deviate from standards. These systems can alert the operator and notify others (even the OEM if permitted and enabled) when abnormalities emerge.
As real-time data is assessed, technical publication content management systems can consume this fault data using an API call, matching the fault code to the correct troubleshooting guide, and returning this information to the operator or maintainer proactively.
The operator or maintainer can trigger an API call to the Maintenance Management System directly from the troubleshooting guide with the metadata to create a Work Order with skills, tools and parts required, as defined in the tech pub. The API call can also trigger the logistics system to order the spare parts and allocate tools to accomplish the repair.
Given the complexity of today’s assets, the growing shortage of technicians and the capabilities for more real-time data integration, technical knowledge (Tech Pubs) can and should play a more active role in today’s asset operations and support strategies.
Making the most of your knowledge assets
Several of SDL’s customers use technical publications and IETP’s to drive proactive maintenance activities and to continuously revise competency training based on real-world use.
Join us at the Los Angeles Airport Marriott on May 14th as some of our customers explore their real-world experiences. Click here to register for this informative event. And if you’re unable to join us in LA, click here to learn more about SDL and our Aerospace & Defense solutions.